Nie tylko samą motoryzacją człowiek żyje, więc tym razem jeden z najświeższych zrealizowanych ostatnio pomysłów.
Pomyślałem, że przydałaby mi się półka. Od tego się zaczęło. Ale wiadomo, że nie taka zwykła półka ze sklepu. Wtedy nie byłoby zabawy. To musi być półka „zrób to sam”. O tak, dla zabawy i satysfakcji. Zrobienie półki z płyty meblowej też nie wchodzi w grę. Przecież co to za wyczyn dociąć kawałek płyty i okleić brzegi. To ma być porządna drewniana półka. Do zrobienia fajnej drewnianej półki potrzebuję skleić deski. A zrobienie tego porządnie oznacza porządne ich ściśnięcie na czas klejenia. I tu pojawił się mały problem bo tak dużego ścisku nie posiadam. Szybki przegląd sklepów i okazało się, że dobry duży ścisk jest dość drogi, a najtańsze nie są godne uwagi. Jeden taki tani ostatnio połamałem. Próbując coś ścisnąć – bez komentarza.
No dobra, ale od czego mam w garażu kupkę złomu, a w głowie milion pomysłów. Tak, dokładnie, postanowiłem, że taki ścisk sobie po prostu zrobię. Szybki przegląd tego co mam, ogólny pomysł w głowie jak chciałbym, żeby to wyglądało i do dzieła.
Jako bazy użyłem profilu 20x20x2. Taki miałem i było go całkiem sporo. Chciałem, żeby rozstaw szczęk był ok. 1 m. Nie był mi potrzebny aż tak duży, ale skoro miałem wystarczająco materiału, to czemu nie. Przecież nigdy nie wiadomo kiedy się przyda.
Skoro pomysł był w głowie, z mojej kupki złomu wyciągnąłem potrzebne rzeczy, pomierzyłem ile czego mam i „na oko” dobrałem wymiary poszczególnych elementów. Zacząłem od wymierzenia i pocięcia elementów.
Większość udało się pociąć szlifierką kątową, jednak w przypadku blachy i grubego na ok. 5 mm płaskownika lepsza okazała się wyrzynarka.
Następnie wszystkie ostre krawędzie usunąłem na szlifierce. Tam gdzie nie dało się dojść szlifierką, zadziorów pozbyłem się pilnikiem.
Wszystkie docięte elementy ułożyłem na stole. Znalazły się tam:
– wspomniany profil kwadratowy,
– dwa kawałki ceownika,
– dwa kawałki blachy 2,5 mm,
– kawałek płaskownika 25×2 mm (a może na 1,5 mm, w sumie to sam nie wiem, nie sprawdzałem),
– kawałek grubego płaskownika ok. 40×5,
– pręt gwintowany M10,
– kawałek pręta gwintowanego M12,
– pręt 12 mm, kilka podkładek,
– tłoczek hamulcowy z Ładnej (oczywiście stary 🙂 )
– kilka nakrętek, w tym jedna M10 przecięta na pół wyrzynarką (później dowiecie się po co).
Uznałem, że powierzchnie dociskowe powinny być zrobione z czegoś bardziej miękkiego niż stal, żeby nie niszczyć ściskanego drewna, dlatego postanowiłem je dociąć ze sklejki. Najpierw odrysowałem kształt, a następnie wyciąłem wyrzynarką.
W drewnianych elementach zaznaczyłem, a następnie wywierciłem otwory pod śruby mocujące.
Następnie pogłębiłem je stożkowym frezem, tak aby łeb śruby schował się w drewnie. Wykorzystałem oczywiście śruby z łbem stożkowym.
Mając gotowe drewniane elementy, zaznaczyłem miejsca pod otwory we współpracujących częściach stalowych, a następnie je wywierciłem.
Ponieważ wiedziałem, że po złożeniu nie będzie możliwości przykręcenia nakrętek „od tyłu”, otwory w stalowych elementach nagwintowałem gwintem M6.
Tak przygotowane elementy skręciłem ze sklejką, a następnie doszlifowałem sklejkę do ostatecznego kształtu, czyli starałem się zrównać jej krawędzie z krawędzią metalu. Niestety moja szlifierka jest trochę za słaba do takich zabaw i nie można zbyt mocno dociskać elementu. Żeby nie tracić czasu wyrównałem tylko brzeg sklejki, nadałem w miarę sensowny kształt i tak zostawiłem. Może w przyszłości zrobię mocniejszą szlifierkę właśnie do takich prac… 🙂
Wracając do ścisku. Skoro wiercę, to będę wiercić dalej. Najpierw na ceowniku, który miał stanowić zakończenie ścisku, zaznaczyłem punkt. Do ceownika miała być dospawana nakrętka, w której znajdzie się część służąca do skręcania ściskanych elementów. Ponieważ miałem w tym celu docięty pręt M12, musiałem wywiercić otwór o średnicy co najmniej 12 mm. Zrobiłem to w 3 etapach wiertłami 5, 8 i 12 mm.
Ścisk miał być uniwersalny, tzn miał mieć możliwość wymiany środkowego elementu na dłuższy bądź krótszy. Dlatego zamiast przyspawać nieruchomą (skręcaną) szczękę do głównego elementu, wykorzystałem kawałek rurki, która idealnie nachodzi na mój profil. Nawierciłem w niej dwa otwory na przelot, podobnie jak w głównym profilu, w celu późniejszego połączenia obu części śrubą. Aby mieć pewność, że oś wspólna otworów przechodzi dokładnie przez średnicę, a nie przez cięciwę rurki, wymyśliłem pewien w miarę prosty patent.
Narysowałem linię, a następnie drugą prostopadłą do niej. Zmierzyłem średnicę rurki i w odległości równej tej średnicy narysowałem trzecią linię równoległą do drugiej. Następnie ustawiłem rurkę na pierwszej linii i przesuwałem w prawo bądź w lewo tak, aby jej krawędź jednocześnie zetknęła się z punktami przecięcia pierwszej linii z drugą i pierwszej z trzecią. Wtedy zaznaczyłem na rurce odpowiadające im punkty i miałem w miarę dokładnie wyznaczoną średnicę. Napunktowałem i nawierciłem otwory oddzielnie po przeciwległych stronach, żeby oszczędzić sobie mozolnego precyzyjnego ustawiania rurki pod wiertarką. Dodatkowo mimo, że planowałem użyć śruby M8, nawierciłem otwory 10 mm. Tylko po to żeby mieć większy margines błędu.
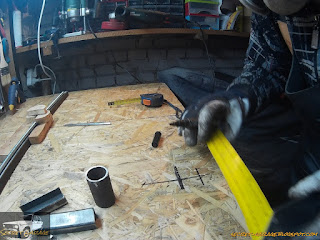
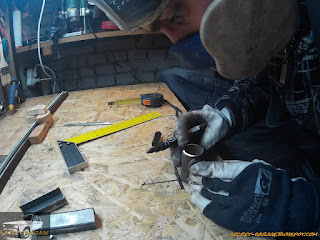
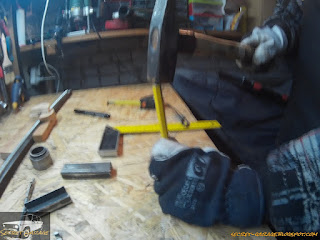
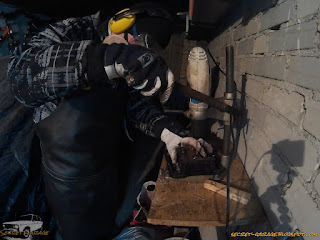
Wszystko powiercone i przycięte, czyli czas spawać. Zacząłem od przyspawania nakrętki, do ceownika. To w niej będzie pracować śruba ruchomej szczęki. Żeby zachować koncentryczność otworu w ceowniku i w nakrętce oraz prostopadłość osi nakrętki do płaszczyzny ceownika, nakręciłem nakrętkę na kawałek pręta, włożyłem do otworu w ceowniku i dokręciłem drugą nakrętką z drugiej strony ceownika. Upewniłem się, że wszystko jest jak należy, a następnie przyspawałem jedną z nakrętek. Kiedy nakrętka była przyspawana odkręciłem drugą nakrętkę oraz pręt.
Następnie wziąłem się za zrobienie szczęki ruchomej. Zacząłem od dospawania pręta gwintowanego do profilu stanowiącego główny element ścisku. Najpierw oczyściłem powierzchnię profilu, aby mieć ładny, czysty metal do spawania.
Pręt należało przyspawać dokładnie na środku tak, aby na całej jego długości ruchoma szczeka mogła się z nim zazębiać. W tym celu, z pomocą gorącego kleju i ścinków drewna, zrobiłem prosty przyrząd, który posłużył do pozycjonowania pręta przed spawaniem. Pręt położony na profilu, pozycjonowany za pomocą przycisku został przyspawany najpierw na końcu. Następnie przesunąłem przyrząd i przyspawałem go w kolejnym i kolejnym miejscu. W sumie pręt został przyspawany na końcach i w trzech miejscach w środku.
Główny element gotowy, więc czas zająć się ruchomą szczęką. Zacząłem od zespawania bocznej blachy ze spodnią. Oczywiście zadbałem o odpowiednie pozycjonowanie i prostopadłość elementów względem siebie.
Elementy lekko przyłapałem tak, aby się trzymały, a następnie wziąłem się za dospawanie drugiej ścianki. W tym celu na ściance z podstawą położyłem główny profil, a na nim drugą ściankę. Elementy przyłapałem i sprawdziłem czy przesuwają się względem siebie bez nadmiernego oporu. Zawsze można było je jeszcze lekko rozchylić.
Teraz przyszedł czas na jeden z głównych elementów tej szczęki, czyli pół nakrętki. Postawiłem szczękę na jej podstawie. Włożyłem do środka połówkę nakrętki, a następnie położyłem profil z prętem gwintowanym tak aby gwint na pręcie zazębił się z gwintem na nakrętce. W ten sposób miałem pewność, że nakrętka będzie prawidłowo zpozycjonowana. W takiej formie przyspawałem nakrętkę do podstawy co, w tej pozycji, nie było może najłatwiejsze, ale za to wydało mi się najsensowniejsze ze względu na późniejszą prawidłową współpracę tych dwóch elementów.
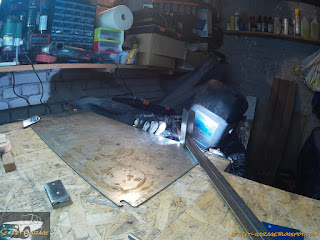
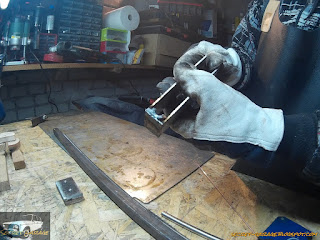
Ruchoma szczęka była prawie gotowa. Zostało dospawanie ceownika z tyłu (to on głównie przejmie siłę nacisku podczas pracy ścisku). Bez wyjmowania centralnego profilu z wnętrza szczęki ustawiłem odpowiednio ceownik względem blach bocznych i profilu a następnie przyłapałem. Sprawdziłem poprawność przestawiania i blokowania szczęki. Wszystko grało jak trzeba więc dospawałem go ostatecznie, podobnie podstawę. Na koniec zostawiłem dospawanie elementu dociskowego szczęki. Ponownie, bez wyjmowania centralnej części ścisku, ustawiłem gruby płaskownik względem ścianek bocznych, przyłapałem małym ściskiem, sprawdziłem poprawność działania szczęki, wyjąłem centralny profil i dospawałem.
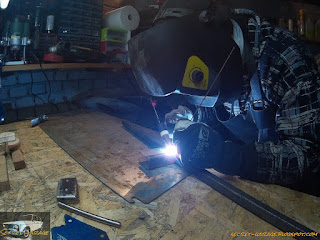
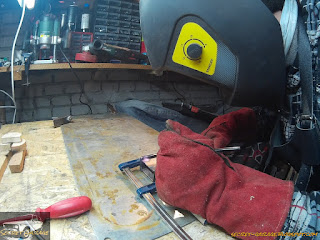
Następnie, na drugim końcu ceownika stanowiącego nieruchomą szczękę, dospawałem wcześniej nawiercony kawałek rurki. Trochę czasu zajęło odpowiednie jego wycentrowanie względem zarówno ceownika jak i profilu, na którym miał być później założony. W końcu oś otworów musiała być prostopadła do ścianek profilu. Tak ułożoną rurkę zabezpieczyłem przed przesunięciem za pomocą małego ścisku stolarskiego i przyspawałem do ceownika.
Później na końcu pręta M12 przyspawałem nakrętkę, która miała mocować tłoczek.
Ze względu na głębokość podtoczenia w tłoczku, za dospawaną nakrętką pojawiła się druga nakrętka i dwie podkładki, a dopiero na nich podkładka powiększana, której średnica zewnętrzna zgadzała się ze średnicą tłoczka. Taki zestaw zapewniał, że tłoczek będzie mógł się obracać względem pręta, ale nie będzie miał za dużego luzu. Zestaw włożyłem do podtoczenia w tłoczku i przyspawałem powiększaną podkładkę do krawędzi tłoczka. Dokręcana szczęka była prawie gotowa.
Pozostało wkręcenie w nią pręta M12 z tłoczkiem, a na jego wolnym końcu dospawanie nakrętki, przez którą przełożyłem pręt 12 mm. Ten element stanowi rączkę do skręcania ścisku. Pręt zabezpieczyłem przed wysunięciem nadlewając trochę metalu na jego końcach.
Teraz pozostało już tylko nawiercenie otworów w profilu kwadratowym, które miały posłużyć do zamocowania nieruchomej szczęki. Założyłem rurkę na koniec profilu, zaznaczyłem i napunktowałem miejsce, w którym należało wykonać otwór, a następnie nawierciłem go, z jednego zamocowania przez dwie ścianki, wiertłem 8 mm.
Ścisk gotowy. Wszystko pospawane, poskręcane i poskładane. Można go jeszcze tylko pomalować, ale temperatura w garażu nie sprzyja schnięciu farby więc zostawię to na cieplejsze dni. Wyszło całkiem nieźle i myślę, że spełni swoje zadanie.
Mam nadzieję, że się podobało. Do zobaczenia 🙂
Podobało się? Podziel się z innymi:
DIY - Zrob to sam, metalworking, narzędzia warsztatowe
bar clamp, DIY, jak zrobić ścisk stolarski, metalwork, metalworking, narzędzia warsztatowe, pomoce warsztatowe, ścisk stolarski, zrób to sam
Opis dla profesjonalistów, ale oni i bez tego wiedzą, jak to zrobić. Psu na budę to potrzebne….
Wydawało mi się, że w miarę jasno wszystko opisałem. Jeśli nie to chętnie odpowiem na pytania. Poza tym ściski można robić na wiele sposobów, a to może być tylko inspiracja, z której ktoś może czerpać pewne rozwiązania. Profesjonaliści też się wspierają różnymi inspiracjami 🙂